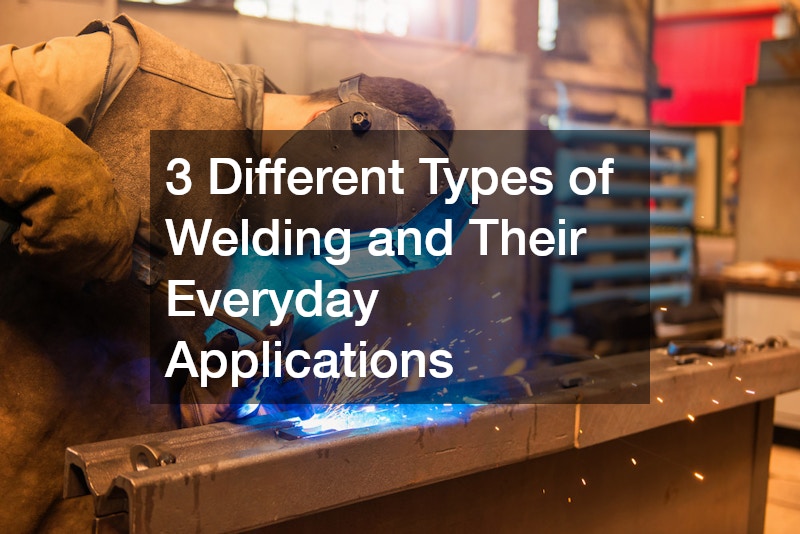
Welding plays a vital role in a wide range of industries, from construction to automotive repair and even home maintenance. This process, which involves joining materials—typically metals—through high heat and sometimes pressure, is more common in everyday life than many people realise.
Whether it’s the framework of a building or the repairs to your car’s exhaust system, welding is often working behind the scenes to keep things functional and secure.
Although there are many methods available, three types stand out for their frequent use across both professional and DIY settings: MIG welding, TIG welding and Stick welding. Each has its own strengths and specific applications, and knowing the difference can help you better understand how the things around you are made and maintained.
MIG Welding (Gas Metal)
MIG, or Metal Inert Gas, is one of the most commonly used forms due to its ease of use and versatility. This method uses a wire that is continuously fed through the welding gun, along with a shielding gas that protects the weld from contamination. Because it’s relatively easy to learn and highly efficient, MIG is a go-to option for many tradespeople and hobbyists alike.
One of the major benefits of MIG is that it produces clean welds with minimal spatter, which means less cleanup. It’s often used for medium-thickness metals such as mild steel, stainless steel and aluminium. You’ll find it widely used in the automotive industry, where precision and speed are both important, especially for assembling car panels and making repairs. It’s also commonly used in manufacturing and household projects like metal furniture or garden gates.
MIG welding is ideal for indoor use because the shielding gas can be affected by wind. This makes it less suited for outdoor work unless proper precautions are taken. However, for controlled environments and projects requiring a smooth finish, MIG continues to be a practical and dependable option.
TIG Welding (Gas Tungsten)
TIG or Tungsten Inert Gas welding is a more advanced technique that requires a higher level of skill and control. It uses a non-consumable tungsten electrode and typically requires the welder to manually feed filler material into the weld puddle. Like MIG, it also uses a shielding gas—usually argon—to protect the weld area from oxidation and contamination.
What sets TIG welding apart is its ability to create high-quality, precise welds. It’s the preferred choice for welding thin materials or working on metals that require a clean finish, such as stainless steel, aluminium and copper. Because of its precision, TIG welding is used extensively in the aerospace and aviation industries, as well as in the production of bicycles, race cars and food-grade kitchen equipment.
While TIG welding is slower and more time-consuming than other methods, the results are often worth it when appearance and detail matter. It also gives the operator more control over the weld, making it ideal for intricate or delicate work. However, it’s not typically used for high-volume production where speed is a priority.
Stick Welding (Shielded Metal)
Stick welding, also known as arc welding or SMAW, is one of the oldest and most versatile methods. It involves the use of a consumable electrode coated in flux, which creates a protective gas shield when heated. This self-shielding property makes Stick welding ideal for outdoor applications and harsh environments, where wind and weather can interfere with other techniques.
Because it doesn’t rely on a separate shielding gas, Stick welding is well-suited for field repairs and structural work. It can be used on a variety of metals, including steel, cast iron and aluminium, and works well even on rusted or dirty surfaces. This makes it a favourite for construction sites, pipeline work and farm equipment repairs.
Although Stick welding requires some experience to master, it remains one of the most accessible forms for beginners and professionals alike. The equipment is relatively simple and portable, which adds to its appeal for mobile welding jobs or locations without access to modern equipment.
Choosing the Right Method
Each of these welding types serves a specific purpose, and the right choice depends on the materials involved, the environment and the desired outcome. MIG welding offers speed and ease, making it great for general fabrication and repair work. TIG welding excels in precision and finish, ideal for detailed or high-end projects. Stick welding offers rugged reliability in tough conditions, especially outdoors or in remote areas.
No matter the method, welding plays a crucial role in maintaining the infrastructure and equipment we rely on every day. From the fences around your property to the car you drive and even the public buildings you enter, welded joints keep everything structurally sound and safe.
Understanding the basics of these different welding methods can help you make better decisions if you’re ever involved in a project that requires metalwork. It can also deepen your appreciation for the skilled tradespeople who use these techniques to build, repair and innovate across countless industries.
Welding is more than just a trade—it’s a foundational skill that supports modern life in countless ways. Whether you’re watching a welder repair a bridge, fabricate a custom trailer or build a metal staircase, you’re witnessing a craft that combines precision, heat and knowledge. With MIG, TIG and Stick welding each offering their advantages, it’s easy to see how this age-old technique continues to evolve and remain relevant in today’s world.